The landing gear - ATA 32 - Part 2
- museedelta
- 15 déc. 2022
- 4 min de lecture
Nose Gear Continued.
The main function of the nose gear is to steer the aircraft when moving on the ground.
The nose landing gear comprising:
- A leg
- A rotatable oleo-pneumatic shock-absorber,
- A steering device actuated by a racked hydraulic jack.
The jack is joined to the shock-absorber by torque links.
The steering device can only be operated when the aircraft is on the ground at a speed below 125 knots.

Torque Links
The torque links are comprised of two half-links pivoted about a hinge pin held in spherical bearings. This installation allows adjustment of axle parallelism in relation to the landing gear articulation axis. In operation, the steering jack movements are transmitted to the shock strut through the torque links integral with the splined sleeve.
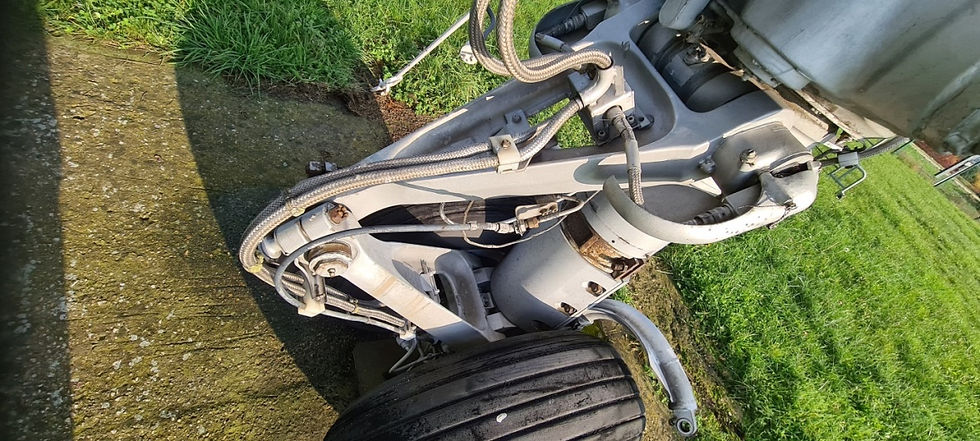

Steering
Steering is provided by a rack and pinion hydraulic cylinder mounted on the front axle strut. The rotational movement is transmitted to the shock absorber strut on which the axle equipped with two wheels is fixed
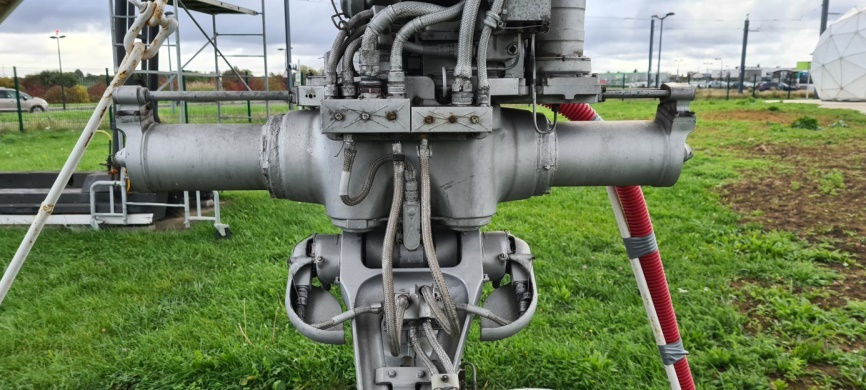

Hydraulic cylinder
The orientation of the front wheels is obtained by means of a double-acting hydraulic cylinder powered by GREEN (or YELLOW) hydraulic pressure, which orients itself on either side of the axis of the aircraft from 60°.

The manoeuvre of the front wheels is controlled by the pilots by means of a steering wheel on the side seat is used for taxiing, or on the pedals used in landing and take-off.

The orientation command is transmitted to the cylinder by an electric chain which delivers a signal to a servo-valve, depending on the difference between the position of the control and that of the wheels detected electrically.
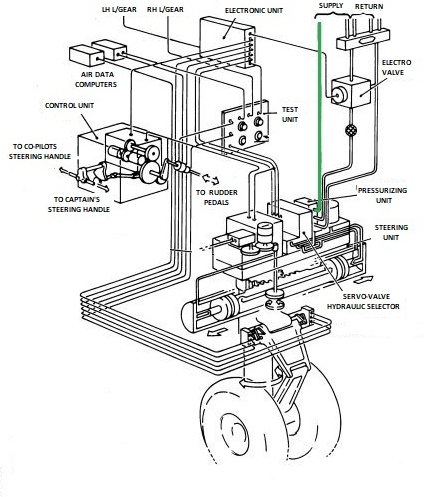
A monitoring chain and a comparator cut off the hydraulic supply to the assembly if an abnormal difference is observed between the orientation order and the position of the servo-valve spool.
The front wheel steering allows making a U-turn on a 39 meter wide track (taking into account wheel slippage). The maximum orientation angle of the wheels is 60°.

Wheels and brakes
The front axle has twin wheels.
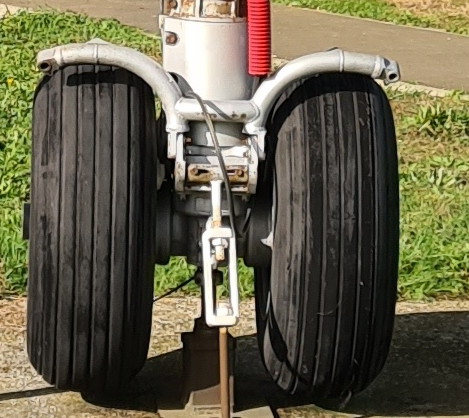
The nose landing gear wheels are fitted with 31x10.75-14 tubeless tyres.
The wheel is made up of two halves assembled with self-locking bolts. The mating surface of the two halves is sealed with an o ring seal. The tyre is removed by removing the bolts and separating the wheel halves. The wheel is fitted with a tyre inflating valve.
The wheels are installed on a splined axle and secured by a nuts crewed on to the end of the axle. The nut is locked with a device that ensures locking even if incorrectly fitted. The wheels are integral with the axle in rotation, and the axle is mounted in taper roller bearings.
A ring gear attached to the axle drives two tachometer generators through two pinions. The two tachometer generators control the SPAD braking system.

On take-off the speed of the plane is over 180 mph and to avoid vibrations it has a braking system that operates when the landing gear retracts.
Nose landing gear wheel braking is achieved by two jaws installed in a yoke which breaks a rotating disc.

Water deflector
This is a stirrup mounted astride the wheel diabolo; its purpose is to avoid side splashes of water. It is attached to the towing fitting, and held by two bearings mounted at the end of the spindle. Each side part is hinged so as to allow removal of the wheel. The lower part consists of a shoe made of frangible material.


On the enlargements taken from various AAMD (DR) archive photos below, the SA was not equipped with deflectors at the start of the flight tests.
Toulouse 1973
![]() | ![]() |
Fairbanks Fevrier 1974 | Gander Décembre 1975 |
This photo from our SA collection (DR) immediately caught our attention.

We remembered the video of Mr. Yves PINGRET test flight engineer (158 flights on the SA) who came to see us in June 2015 with his “little children” of which here is the transcription of his explanation.
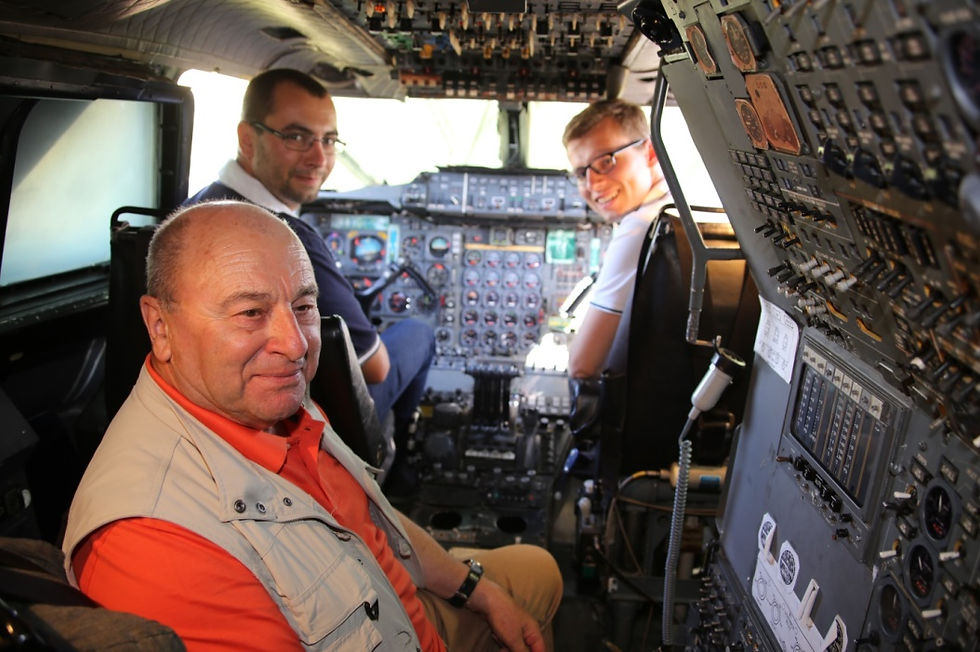
"When we went to Anchorage, we were moved one runway, the good one was snow cleared and the worst one was full of slush, that is to say water with ice of a certain thickness and we were authorized to take off from this runway.
During the take-off phase of course there was water ingestion and "slush" in the engines since we had no wheel protection at the time, shut down two engines in the middle of the take-off phase and luckily we had the automatic re-ignition which was working which allowed us … the engines restarted on their own and we saved the plane and ourselves. »
Editor's note
It was flight 113 on February 15, 1974 (4th flight of the cold weather campaign)
The crew was composed today by:
Pierre DUDAL* (CEV), Jean FRANCHI, Pilots
André TURCAT, Observer
Yves PINGRET, Flight test engineer
*Air France captain, seconded to the Flight Test Center as a test pilot, after his return to AF he will be the first Concorde sector manager.
Don't miss this flight described by Pierre DUDAL on the "Les vols de Concorde" website.
(Select “vols” then “F-WTSA” in the list of flights, the flight “113” and then "Anecdotes")
We contacted Mr. PINGRET a few days ago to ask him to comment on the photo above.
The next day, he called us back and as always with so much kindness he finished the story told above.
“And on returning to Toulouse, we carried out several “pool” tests corresponding to the Anchorage breakdown,
- With the nose wheel,
- The main gears and
- All,
This is how the water deflectors subsequently installed on all aircraft were developed.
As for your question about the orange bar across the nose gear:
it supported test equipment that was mounted on it. »

As you can see on the following photos the deflectors are absent on the SA and the fitting which is used to hook the tow bar which is used here to fix the front axle to the jack which keeps the tires above the ground.

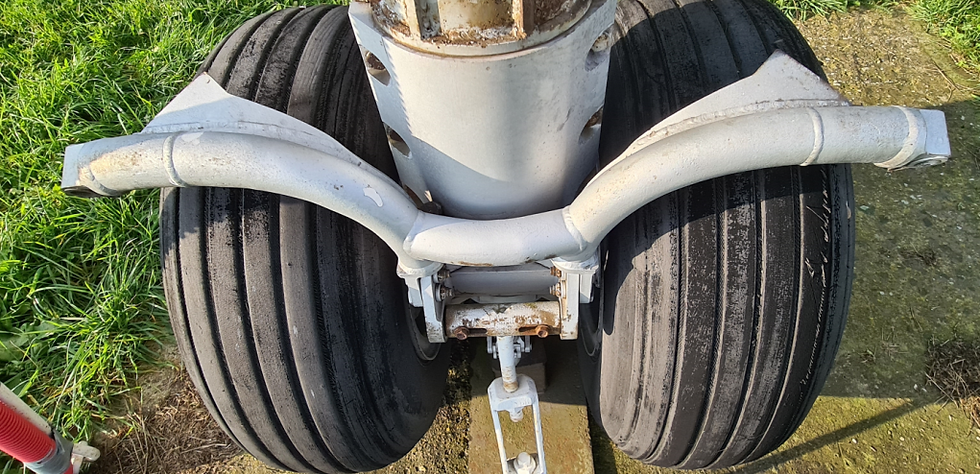

Fitting for towing
In this configuration the turning arc is limited to 60 degrees, from one side of the shock strut to the other.
The coupling fitting is integral with the lower part of the steerable nose gear and makes it possible to fix a tow bar which will serve as a link to the runway tractor to ensure the movement of the aircraft as well as the push back after the boarding of passengers at the departure of a flight..
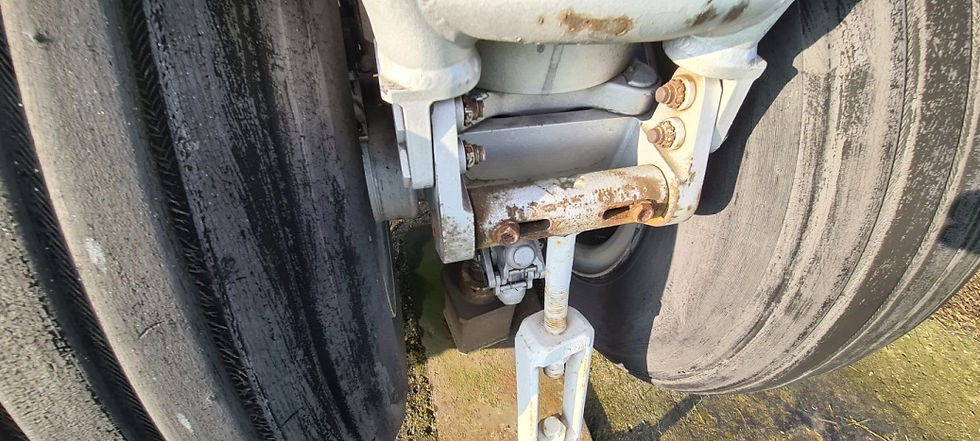

A big thank you to Mr. Yves PINGRET for his contribution to this article and this little personal message "We are counting on you on September 26, 2023"
The nose landing gear emergency lowering will be presented in the last chapter.
To be continued…
Commentaires